Changing mindsets by transforming how tasks are executed and how organizations function
Japan Group is committed to advancing MSV by increasing EPS through productivity enhancements. To achieve this, we are wholeheartedly embracing organizational and human resource management transformation. We are conducting a fundamental review of our organizational structure and task execution methods, while also fostering a change in the mindset of every employee.
As an example, in early FY2021, Japan Group embraced a Japanese iteration of Lean for Growth (J-LFG), which offers actionable guidelines and encourages a mindset shift towards the future, drawing inspiration from the LFG culture established in NIPSEA Group. We proceeded to convene meetings and engage in management communications within our offices and factories to further enhance employees' grasp of J-LFG. Additionally, we took various actions to identify ineffective tasks and processes, subsequently eliminating those deemed suitable for optimization, in accordance with Lean principles.
The resources freed up through these initiatives are allocated towards endeavors that bolster our future growth (Growth), including the development of customer-centric products, enhancement of service quality, and the upskilling of our workforce. Furthermore, we introduced the J-LFG Awards program to acknowledge teams and individuals who have made significant contributions to business and organizational growth through the successful implementation of J-LFG principles.
J-LFG Awards for teams and individuals driving business and organizational growth through J-LFG practices
J-LFG Awards acknowledge teams and individuals advancing business and organizational growth through J-LFG practices. This program encompasses teams and individuals across all divisions and job categories, spanning production, sales, research and development, as well as planning and administration. Employees in Japan Group, including those affiliated with sub-subsidiaries of Nippon Paint Group, have the opportunity to seek recognition for the award through either self-nomination or nomination by their colleagues. A panel selects the winners by evaluating their accomplishments and evaluating their commitment to embodying the principles of J-LFG and VITALS.
The overview of J-LFG
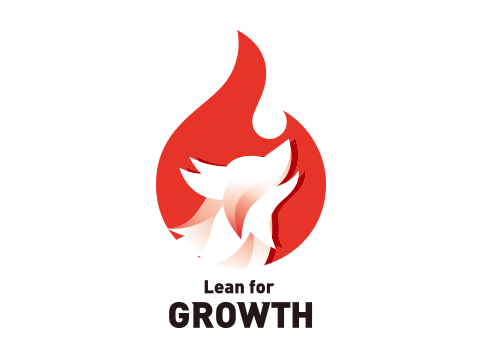
J-LFG (Lean For Growth)
To excel in delivering greater added value to our customers at a swift pace compared to our competitors, all our employees are dedicated to fostering a positive and lean culture aimed at Maximization of Shareholder Value (MSV), regardless of the prevailing business conditions. This commitment results in surplus resources that can be allocated toward initiatives that fuel our growth.
VITALS: The six values and behaviors underpinning Lean for Growth (LFG)
Vigilance | Keep your eye on the prize | Be prepared, be responsive, ever ready |
---|---|---|
Insatiable appetite | Hunger for more | Be ambitious, eliminate complacency |
Teamwork | Work as one | Be strong together, be collaborative, no silos |
Agility | Sense & respond fast | Be nimble, outwit the competition |
Leanness | Back to basics | Be value-driven, be tenacious, make every bite count |
Stamina | Can’t stop, wont’ stop | Be relentless, be resilient, unending quest |
Voices of the Award Winners
J-LFG Awards 2024 Voices of the Winners
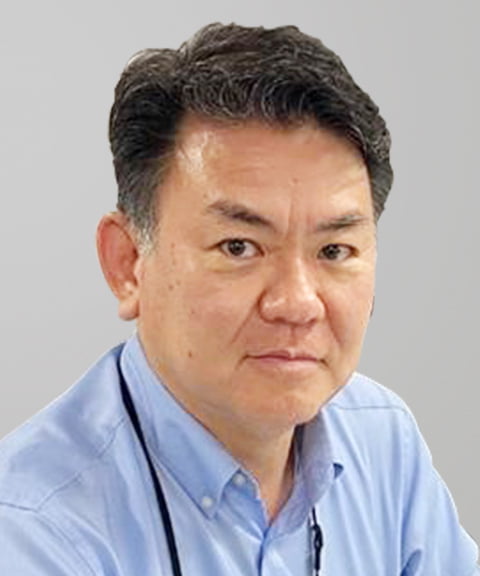
Strengthened Profitability Through Cross-Functional Efforts
Amid Escalating Raw Material Prices
Gold Award Winner: Taisuke Fukumoto (Team Representative)
Nippon Paint Marine Coatings Co., Ltd.
Corporate Services Department
The Sales Division also took proactive steps to offset rising costs, implementing group-wide initiatives to manage raw material price volatility. As a result, year-on-year sales increased significantly, the raw material cost contribution (RMCC) ratio to sales declined, and overall profitability improved markedly. By closely tracking daily price movements of key materials, particularly copper and zinc, which posed the greatest challenges, we were able to anticipate risks and deploy timely countermeasures. These outcomes were driven by cross-functional collaboration, including the exchange of ideas across departments, rigorous monthly reviews of progress and effectiveness, and enhanced coordination with NPMJ, global procurement teams, and technical divisions, all of which contributed to substantial profit gains.
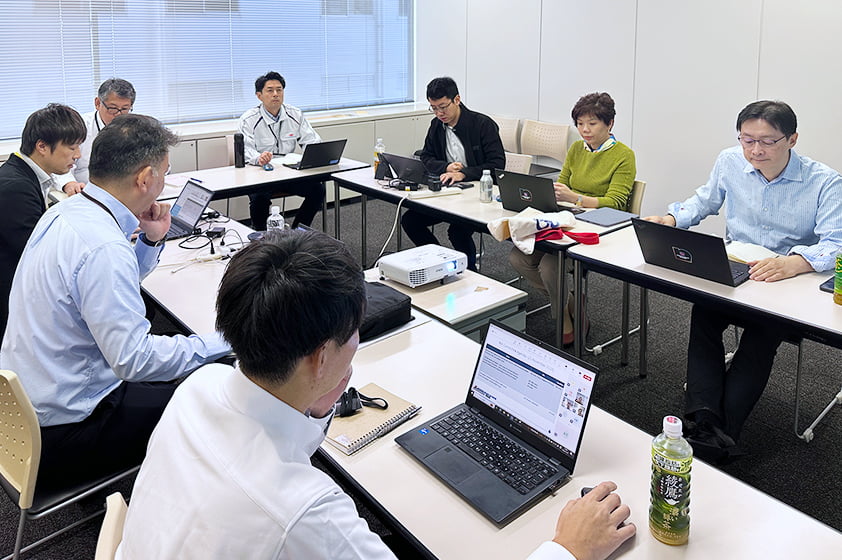
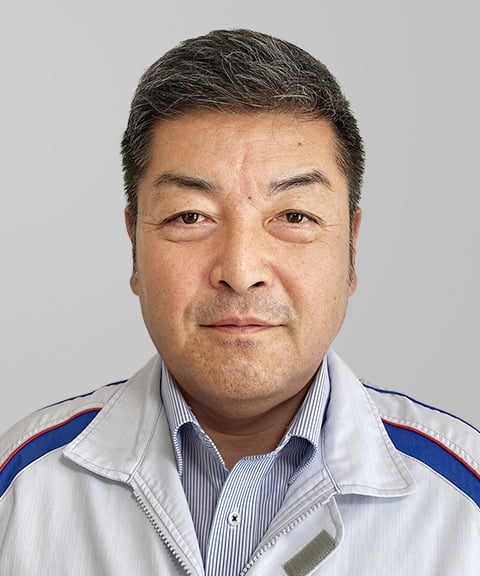
Approval Obtained for Preprocessing and
Electrodeposition Coating for EV Battery Case
Silver Award Winner Yoshiaki Nakajima (Team Representative)
Nippon Paint Automotive Coatings Co., Ltd.
Toyota Group Sales Department,Toyota Line
While exploring new business opportunities, we identified a customer preparing to introduce preprocessing and electrodeposition coating lines specifically for battery cases used in battery electric vehicles (BEVs). Recognizing the growth potential in this sector, we made a strategic commitment to pursue the opportunity and deliver tangible value. To differentiate ourselves, we emphasized our integrated capability to manage both preprocessing and electrodeposition processes, our proven track record with existing production lines, our high level of technical support, and our consistent quality and reliability. One of the most significant challenges during the project was adapting to a change in the originally specified preprocessing agent. To address this, we collaborated closely with internal teams to evaluate alternative materials, perform technical assessments, and implement necessary design modifications, all while staying on track to meet the customer’s mass production schedule. As a result of this collective effort, we successfully secured new production lines in the EV segment, marking our entry into a new market, and laid the groundwork for future global expansion. By sharing the knowledge gained and providing feedback on the challenges encountered, we remain committed to accelerating the Group’s global growth in this promising field.
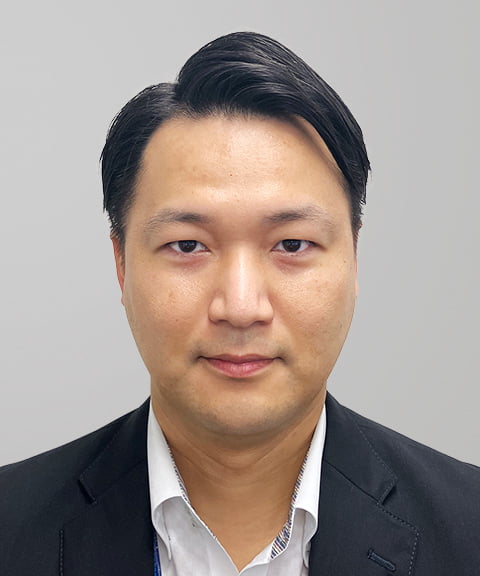
Development and Promotion of Insulation Coating Specifications for
EV Battery Components
Silver Award Winner: Tomoya Shiba (Team Representative)
Nippon Paint Industrial Coatings Co., Ltd.
Sales Division, New Market Development
We spearheaded the development and promotion of insulation coating specifications for EV battery components. In response to emerging requirements for enhanced insulation performance, we formulated epoxy resin-based powder coatings by integrating expertise from our overseas group companies. As some of the EV components were newly designed by the customer, their quality standards evolved frequently. By responding with agility, collaborating closely with our domestic group companies, and drawing on expertise from across and beyond the organization, we successfully developed tailored solutions in a short timeframe. Looking ahead, we remain committed to technological innovation and value creation, striving to achieve the optimal balance between cost and performance, while also expanding the application of these solutions to other EV components.
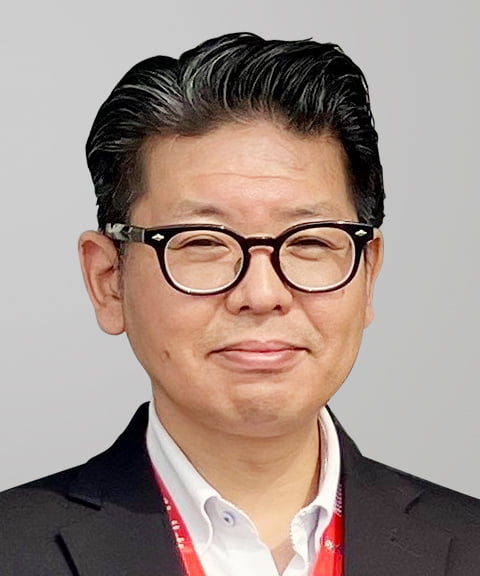
Fundamentally Rebuilding a Strong,
Streamlined Production and Logistics Base
Bronze Award Winner: Kenji Oikawa (Team Representative)
Nippon Paint Co., Ltd.
Supply Chain Strategic Planning, Innovating Promotion Office
Following the 2015 business line-based corporate split (bunshaka), each domestic group company independently optimized its production and logistics functions to align with its specific business needs, thereby strengthening individual capabilities. However, this restructuring also resulted in certain inefficiencies across the Group.
To address these challenges, we recognized the need to rebuild a more efficient and robust production and logistics foundation. In response, we established the Production and Logistics Integration Committee, tasked with driving initiatives such as factory operation process integration, productivity enhancement, talent development, and logistics optimization. We set an ambitious target, to reduce manufacturing and logistics costs by over ¥2 billion within three years. Through these efforts, we achieved substantial improvements across the Group, enhancing efficiency while preserving the unique strengths of each company. This required striking a careful balance between group-wide integration and company-specific optimization, and promoting the sharing of best practices and management resources.
Committee members led these initiatives alongside their regular responsibilities, delivering meaningful results. I believe our success stems from a shared commitment to making our company better, realizing our vision for the future, and a deep sense of pride in supporting our position as a leading manufacturing company.
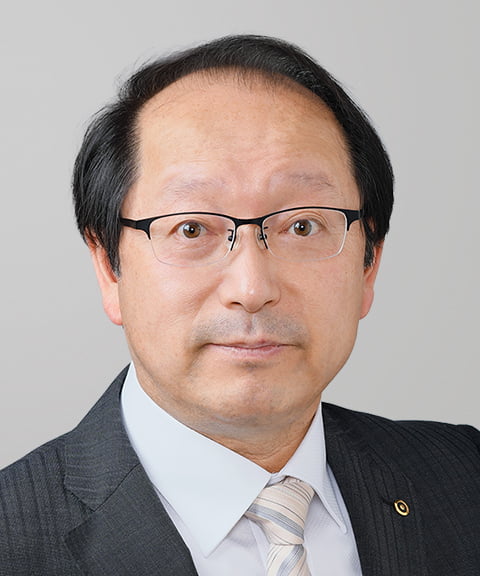
Driving Waste Reduction Initiatives Across Manufacturing
Encouragement Award Winner: Nobuyuki Watanabe (Team Representative)
NPA MFG CO., LTD.
Company President
A distinguishing feature of this initiative is its focus on quantifying reductions in labor hours and expenses, enabling centralized management and organization-wide sharing of results. This approach allows us to monitor the progress and specific activities taking place at other sites. Enhancing production efficiency within constrained labor resources remains an ongoing challenge in manufacturing. By fostering a data-driven mindset through this initiative, we aim to apply these insights more broadly across our overall business operations and management practices.
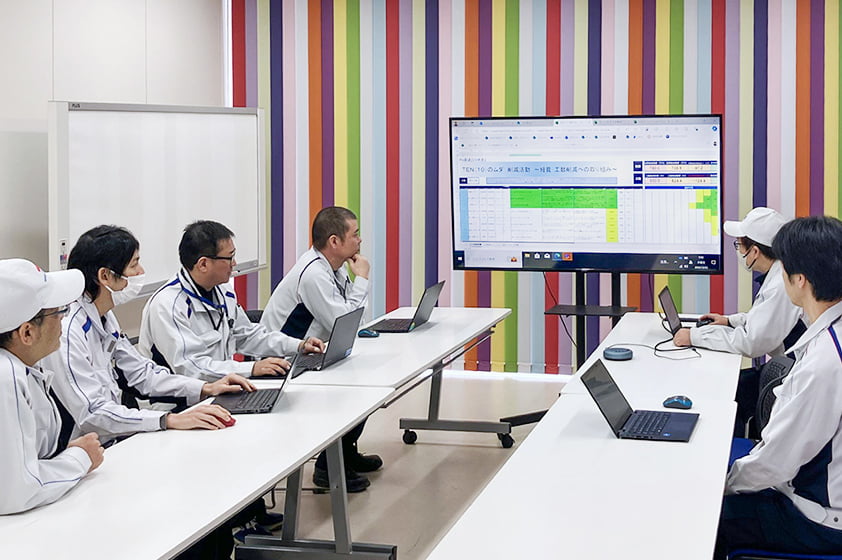
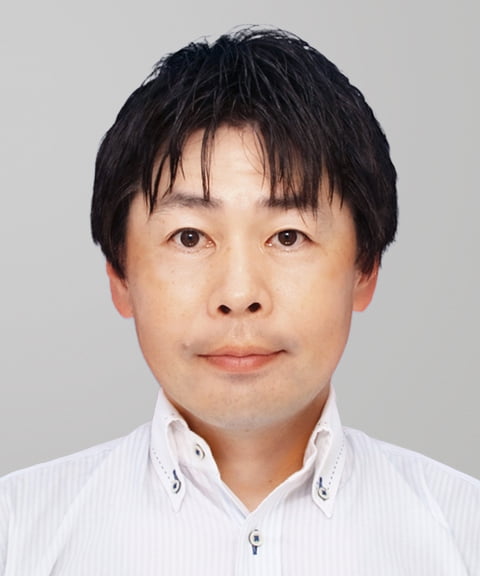
Embedding DOE for Systematic Experiment Design,
Execution, and Evaluation
Encouragement Award Winner: Hiroyuki Suzuki (Team Representative)
Nippon Paint Industrial Coatings Co., Ltd.
Technology Division, R&D & New Business, Core R&D Group
Members of the Data Science Technology Network, comprising representatives from each group company, collaborated to tackle shared, company-wide challenges in data science. A key objective was to promote and institutionalize the use of Design of Experiments (DOE), particularly for product and process optimization. Past efforts to introduce DOE revealed three primary obstacles:
- Unavailability of free, user-friendly tools for designing and analyzing experiments
- The theoretical complexity of DOE, which hindered widespread understanding and adoption
- Difficulty in envisioning practical, real-world applications
To address these challenges, we implemented the following initiatives:
For the first issue, we developed and distributed a free DOE software tool to make experimental design and analysis more accessible.To tackle the second, we produced intuitive, beginner-friendly educational videos and made them available on our internal portal to simplify the learning curve.For the third, we incorporated successful case studies from each group company into our training materials, launched short-term training programs, and promoted early adoption by showcasing exemplary applications at achievement presentations.By embedding DOE practices across the organization, we aim to further enhance and streamline our technical activities. This will strengthen our competitive edge, create new market value, drive sustainable sales and profit growth, and contribute to building a robust, resilient organization.
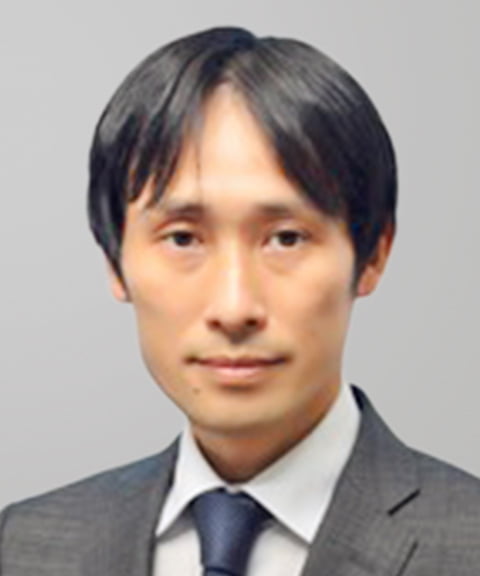
Driving Operational transformation and Enhancing IT Literacy
through the Introduction of Generative AI
Encouragement Award Winner: Tomohiro Kondo (Team Representative)
Nippon Paint Corporate Solutions Co., Ltd.
Information Technology & Solutions, Strategic Planning
To enhance employees’ IT literacy and operational efficiency, we introduced the generative AI tool “NP ASSISTANT.” In collaboration with Nippon Paint Automotive Coatings Co., Ltd., where the tool was first piloted, and the IT Case Study Presentation Secretariat, we actively promoted AI adoption by organizing training programs and establishing a framework for sharing practical use cases. Since its launch, both the number of users and frequency of use have grown significantly, with more advanced applications, such as integration with internal data and image-based inputs, now being implemented across the organization.
During the adoption of Retrieval-Augmented Generation (RAG) technology, we encountered challenges in data organization and accuracy enhancement. However, through targeted training and rigorous technical validation, we successfully developed AI-driven tools such as the “AI Dictionary” and the “Legal Department Chatbot.”
Looking ahead, we remain committed to building systems that empower employees to actively integrate AI into their daily work.
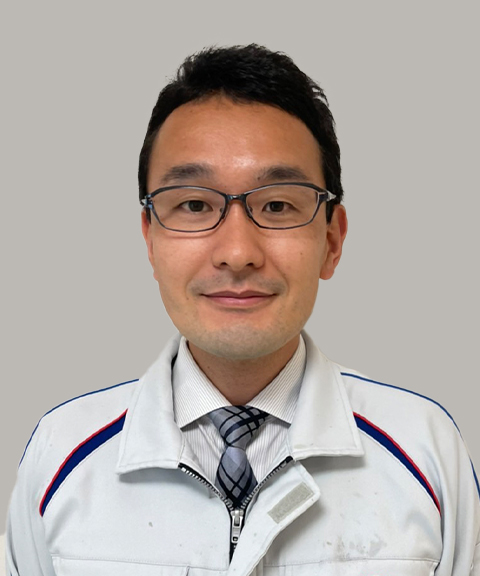
Enhancement and Advancement of the SMP Program in Japan
Gold Award winner: Takeshi Hara (The Spokesperson for the Award Winners)
Nippon Paint Corporate Solutions Co., Ltd.
Operational Excellence Department, Supply Chain Division, Planning and Control Group
"Production quality" is a top priority for us as a paint manufacturer. Ensuring consistent quality requires managing various influencing factors and potential risks. Since the 1990s, we have implemented the Strong Manufacturing Program (SMP), a unique initiative aimed at enhancing production quality. However, following the bunshaka restructuring, opportunities for information exchange between our Group partner companies decreased, causing a decline in SMP activities. To counter this, the production units within Japan Group have come together once more to revitalize the SMP activities, with a renewed focus on improving production quality.
The specific activities within the SMP initiative are detailed below. Furthermore, the daily efforts of our production team members to drive continuous improvement form the foundation of the SMP program.
- Visualizing progress and outcomes through the SMP dashboard
- Measuring production quality at the operational level and setting specific targets for each factory, based on thorough diagnostics conducted by SMP advisors, who specialize in production quality
- Developing human resources by creating an effective learning environment and reinstating the Global Quality Convention
- Promoting personnel exchanges through regional networking events in the eastern, central, and western areas
Revitalizing the SMP activities has led to a notable reduction in significant quality abnormalities and customer complaints, resulting in enhanced production quality across all our companies. This improvement aligns with the core philosophy of J-LFG, which is to "promptly provide customers with superior value compared to our competitors."
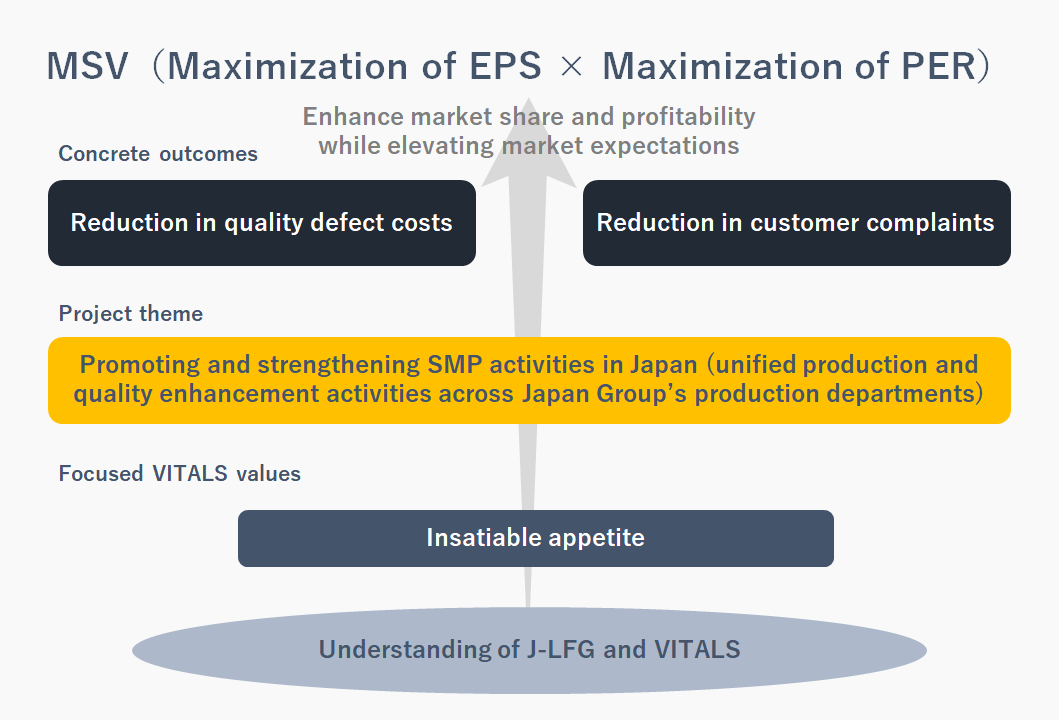
This success is credited to the "insatiable appetite" for enhancing SMP activities exhibited by all production team members and promotion leaders in Japan, driven by the VITALS spirit. The comprehensive understanding of SMP's importance and the proactive participation of each production team member transformed the initiative into a nationwide movement. This collective effort across all production teams in Japan has been a significant factor in our success.
Looking ahead, we plan to broaden the scope of SMP activities to include other divisions within our organization. Furthermore, we will actively share expertise and best practices with our overseas partner companies to further enhance our production quality.
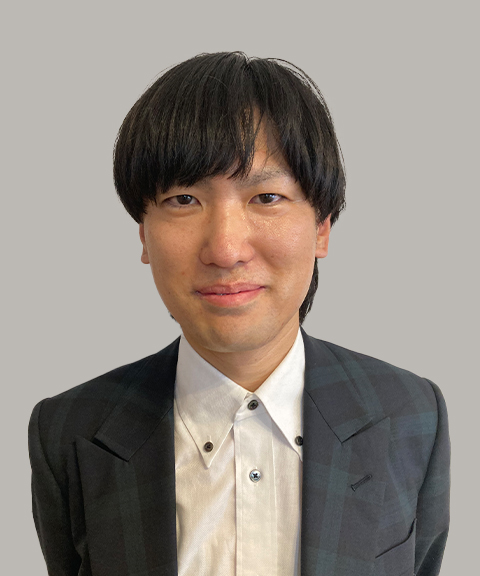
Entering and Strengthening Market Position in the Autonomous Driving Industry through Strategic Target Line Paint Promotion Initiatives
Silver Award winner: Masashi Kasagi (The Spokesperson for the Award Winners)
Nippon Paint Industrial Coatings Co., Ltd.
Sales Division, New Market Development Department, Road White Line Team
We have successfully created "Target Line Paint" specifically designed for autonomous driving, significantly boosting our presence in this sector through our promotional efforts. This groundbreaking paint allows LiDAR sensors on autonomous vehicles to detect and follow the road lines it forms.
Throughout the development process, we operated with a forward-thinking mindset: "Our aim is to sell paint, but functioning only as a paint supplier restricts our access to crucial information, ultimately limiting the value we can offer our customers." Motivated by the "insatiable appetite" values of VITALS, we chose to participate in the consortium as a key player in autonomous driving demonstration tests, rather than merely acting as a paint supplier. This proactive involvement enabled us to gather extensive insights and maintain a competitive edge from product development to marketing.
Moreover, several municipalities chosen for the 2022 Ministry of Land, Infrastructure, Transport, and Tourism’s subsidy project, “Subsidy for Regional Public Transportation Securement, Sustentation, and Improvement Projects (Autonomous Driving Demonstration Test Project),” have opted to incorporate Target Line Paint into their systems. Additionally, Target Line Paint has been selected for use in transport systems at the upcoming Osaka Expo. This development offers a prime opportunity to expand our business globally, attracting potential customers both in Japan and worldwide.

In anticipation of the rise of an autonomous society, we are committed to advancing Target Line Paint through both technological innovation and strategic marketing. Our goal is to introduce new, paint-enabled solutions that address emerging needs in this evolving landscape.
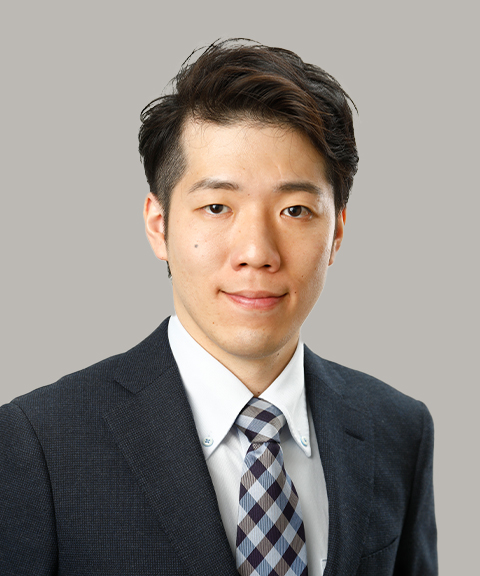
Cross-organizational Development Activities for Anticorrosion Technology
Bronze Award winner: Kengo Tomioka (The Spokesperson for the Award Winners)
Nippon Paint Co., Ltd.
Technology Division, Technology Management Department
We have been promoting technological collaboration among our group companies, both domestically and internationally. In 2023, we concentrated on enhancing the overall success of our Japan Group, emphasizing Leanness (organizational efficiency) and Agility.
Starting from scratch to launch a platform of activities, in collaboration with experts and members from our group partner companies across various business domains, was both rewarding and challenging. After numerous internal discussions and proposals, we successfully established a solid foundation. Our resilience and determination to persevere were crucial to our success.
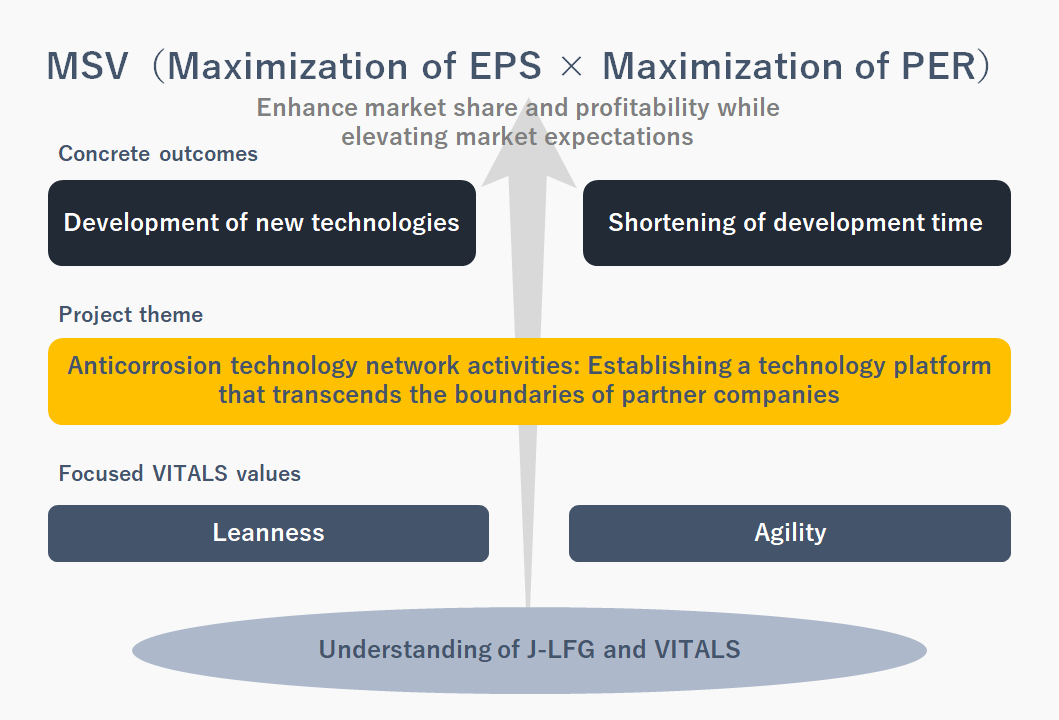
Looking ahead, we will persist in tackling challenges across organizational boundaries to showcase technological synergies.
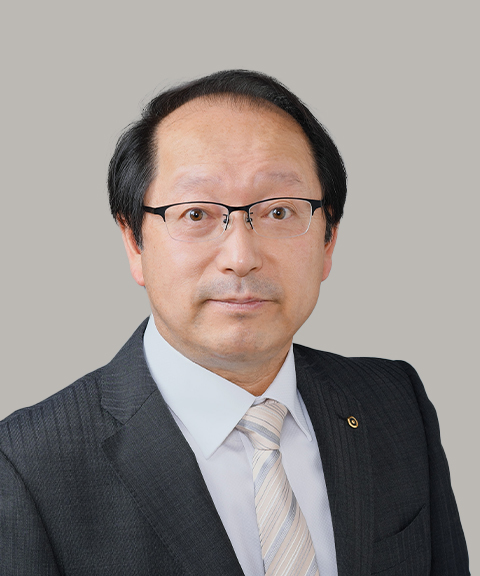
Human Resource Development and Major Reductions in Costs and Man-Hours through Small Group Activities and Operational Enhancements
Encouragement Award winner: Nobuyuki Watanabe (The Spokesperson for the Award Winners)
NPA MFG CO., LTD.
Company President
In this project, we successfully developed human resources and achieved substantial reductions in costs and man-hours by addressing various themes, including next-generation talent development, cost efficiency improvement, and CO2 reduction. These activities were carried out in small groups over short periods, with regular outcome reporting. Our efforts were driven by the VITALS values of Leanness (organizational efficiency) and Teamwork.
In recent years, we have faced significant challenges in our business environment, including (1) a decline in profit due to the impact of the pandemic, (2) a shortage of successors, and (3) rising utility costs. To remain resilient and capable of overcoming these challenges, it is crucial to develop next-generation leaders at the foreman level and promote daily improvement activities among all employees. To achieve this, we implemented a company-wide cycle of (1) generating ideas, (2) analyzing the situation, and (3) taking actions. This approach led to “creating opportunities for employees to think and act on their own initiatives” and “significantly reducing costs and man-hours.” Additionally, by highly recognizing and rewarding employees who strive for excellence, we have successfully embedded these activities into our continuous practices. The major activities are as follows.
-
Small Group Activities
We launched a program where project members collaborated with relevant departments to address issues related to cost reduction, man-hour reduction, and environmental improvement within a concise, four-month cycle. This initiative aimed to enhance human resource development by strengthening employees' skills in idea generation, critical thinking, and negotiation. Feedback was provided by the factory manager, the President, and corporate officers. -
Energy-Saving Promotion Activities
To address rising energy prices and our goal of achieving carbon neutrality, we solicited approximately 200 suggestions for energy-saving measures. These initiatives led to significant cost reductions, saving several million yen compared to 2022 levels. -
Reinstating the Operational Reform Suggestion Program
We reinstated the operational reform activity program to involve all employees in continuous improvement initiatives. By the end of September 2023, we received 1,329 suggestions aimed at reducing Raw Material Cost Contribution (RMCC) ratio.
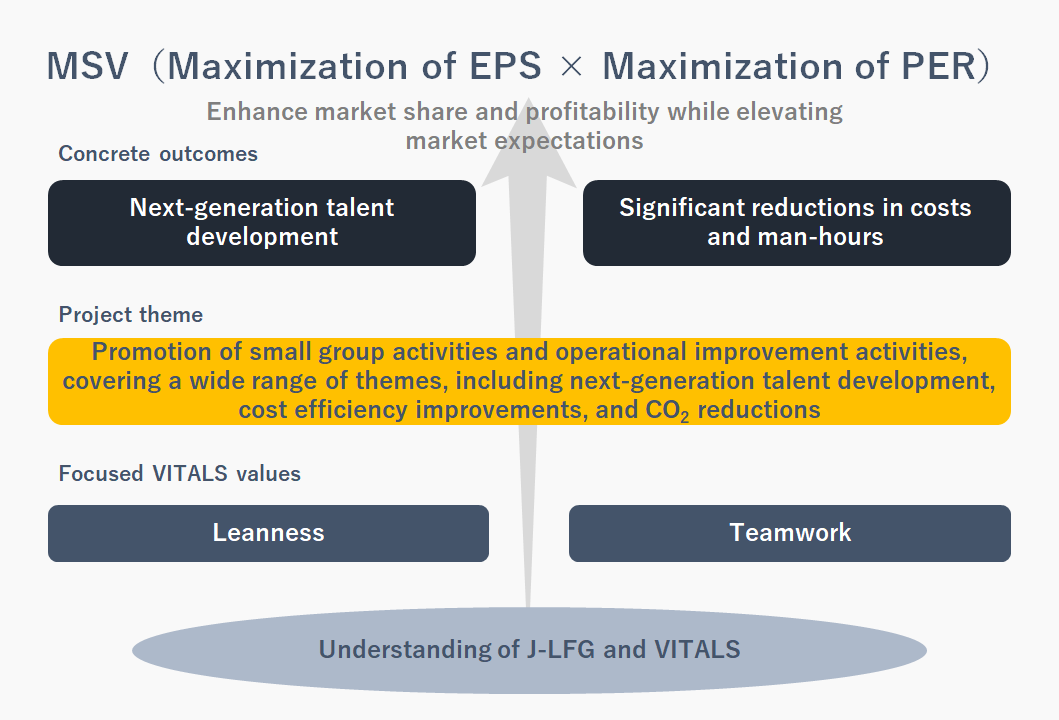
We believe that challenging environments offer significant opportunities for growth and transformation into a resilient organization. The experiences and efforts required to overcome these hardships will undoubtedly bear fruit in the coming years. Our commitment is to generate profits through the collective efforts of all employees, with the ultimate goal of becoming a stronger and more resilient company.
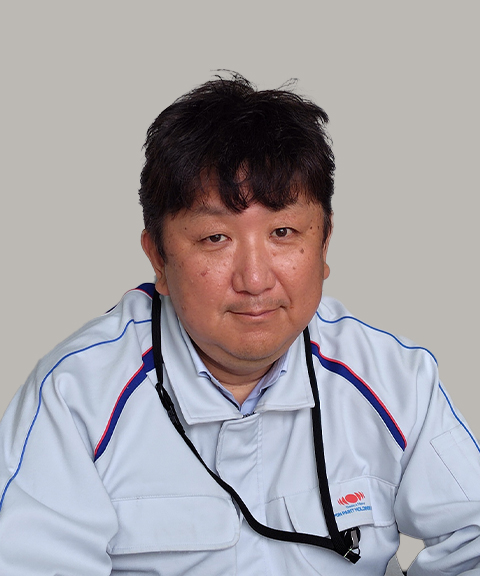
Cross-Departmental Collaboration Challenges in West Japan Logistics and Color Creation Group
Encouragement Award winner: Takeshi Shichiryousako (The Spokesperson for the Award Winners)
Nippon Paint Co., Ltd.
Production and Logistics Division West Japan Production and Logistics Department
West Japan Logistics and Color Creation Groups of Nippon Paint Co., Ltd. conducted cross-departmental collaboration activities embracing the VITALS values of Teamwork and Leanness. Facing significant changes in both internal and external business environments, including rising costs and sluggish market conditions, reducing expenses in logistics, color creation, and other areas has become a critical challenge. To address this, we have actively promoted cross-departmental communication and collaboration to prevent silos, with the goal of maximizing not only our department's profits but also the overall profitability of the company.
Initially, this initiative might not have seemed advantageous from the perspective of our own department. However, by prioritizing the company's overall profitability, each department contributed to the successful completion of the project. Looking ahead, we plan to extend these project activities nationwide, beyond West Japan, to further embody the VITALS values on a company-wide scale.
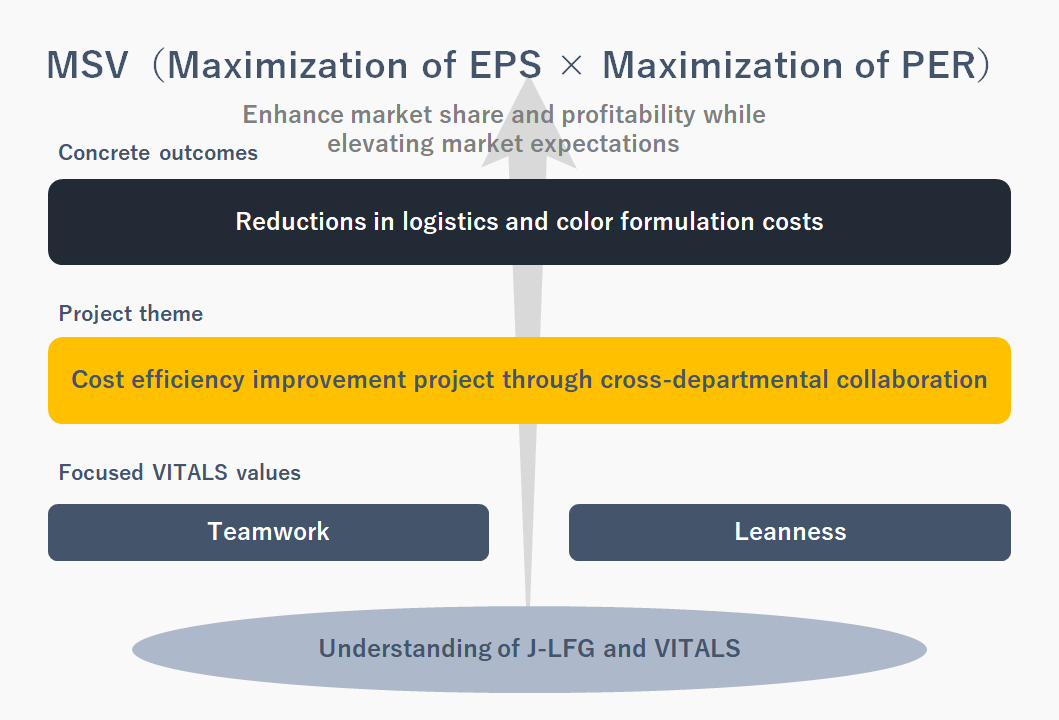
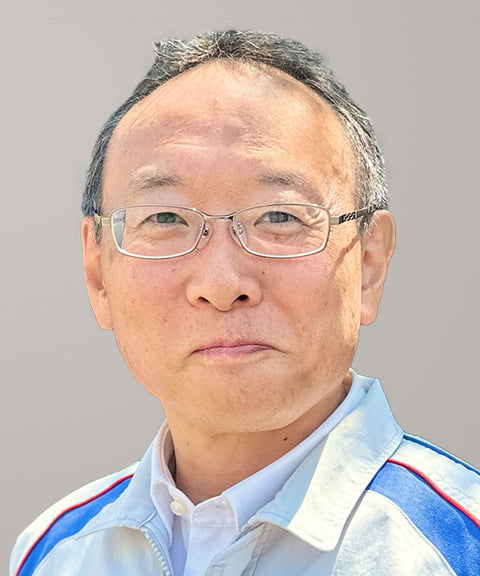
An Efficient Raw Material Management System to Ensure a Stable and Cost-Effective Procurement of Materials
Gold Award winner: Akihiro Sawaguchi (The Spokesperson for the Award Winners)
Procurement Technology Department, Technology Division,
Nippon Paint Industrial Coatings Co., Ltd.
The theme of the project is to develop an ICT tool that facilitates stable raw material procurement at reduced costs, enabling Nippon Paint Group to maximize growth and profitability, irrespective of the business environment. We used ICT tools to centralize information about raw materials and products, which had previously been unevenly accessible and only to designated individuals. Centralizing this information allows for swift and effortless reviews and approvals from various angles, encompassing all functions, including procurement operations, even in emergency situations. The outcome is a framework designed to enhance profitability promptly by utilizing substitute raw materials. At the core of this framework lies an analysis that involves comprehensive comparisons between the standard and actual prices of substitute raw materials in relation to the price of the materials currently in use. We intend to leverage this tool to overhaul our business processes by engaging multiple departments in partner companies and our key suppliers.
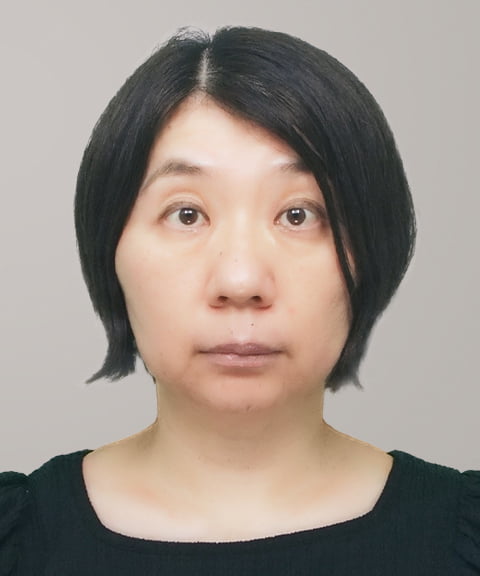
Optimizing Marine Supply Chain Structures for Cost Reduction
Silver Award winner: Aiko Ikeda (The Spokesperson for the Award Winners)
Operations Group,
Nippon Paint Marine Coatings Co., Ltd.
The winning of this award is attributed to our dedication and the substantial profit contributions achieved through our unwavering pursuit of the finest and most efficient solutions, without merely adhering to established precedents. Guided by the theme “Project True GSCM (dedicated to genuine global supply chain management),” our team focused on adapting to market dynamics and customer needs to optimize production, logistics, and inventory management. Our project integrated all the elements of VITALS while remaining unbound by precedent to generate new value. Leveraging our experience, we aim to seek the finest and most optimal solutions, extending our efforts beyond Japan to a global scale within the entire group.
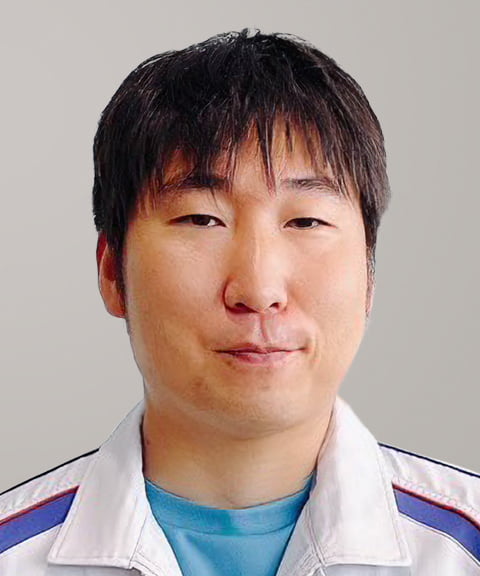
Developing and Introducing Eco-Friendly Low VOC Clear O-4100
Bronze Award winner: Tomoyuki Ishikawa (The Spokesperson for the Award Winners)
Project X Low-VOC2K Clear Team,
Nippon Paint Automotive Coatings Co., Ltd.
This project was undertaken by a dedicated team comprising members from different production bases and countries, united by their commitment to achieving results within an exceptionally short development timeline. We are confident that our robust teamwork and unwavering commitment to meticulous attention to detail until the project’s completion were acknowledged as embodying the “Teamwork” and “Stamina” elements of VITALS. Nonetheless, we are of the opinion that our accomplishments were not solely attributable to our conscious adherence to “J-LFG,” but rather stemmed from our dedicated efforts deeply rooted in the manufacturing philosophy that resonates with both the spirit of J-LFG and VITALS.
Some might believe that adhering to J-LFG and VITALS necessitates distinct activities and accomplishments. In fact, all initiatives undertaken in accordance with our Purpose are inherently linked to J-LFG and VITALS. Therefore, let's engage in proactive discussions about how we can embody VITALS, acknowledge and praise our strengths, and strive to make our Group the global leader.
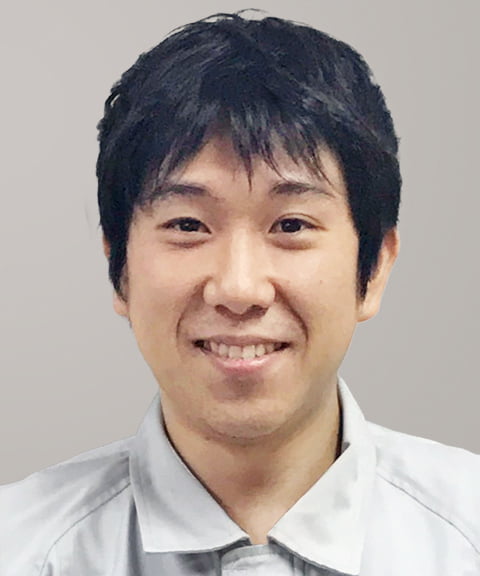
Commencing the Use of Recycled Raw Materials to Increase Profitability and Uphold an ESG-Focused Approach to Management
Bronze Award winner: Keisuke Yoshida (The Spokesperson for the Award Winners)
Joint team for technology, production, and procurement,
Nippon Paint Surf Chemicals Co., Ltd.
Given the rapid changes in the social landscape in recent years, we have recognized the importance of securing supply chains and contributing to corporate growth and ESG as a key focus area for our Group. Accordingly, we have undertaken initiatives with a specific emphasis on the raw materials we use. In this project, participants from various divisions including procurement, technology, planning, and production collaborated to foster cross-functional awareness of pertinent issues. Together, they embarked on a mission to implement J-LFG action guidelines that not only benefit society but also contribute to corporate growth.
I am confident that all team members adhered to VITALS, embracing the values and behaviors that form the foundation of J-LFG. This project held enormous importance as every member assumed a leadership role in executing initiatives aimed at addressing diverse challenges, such as cost-efficient procurement and consistent quality. These efforts were underpinned by comprehensive surveys and analyses, giving rise to unique ideas and opportunities by breaking away from conventional paradigms. This marks not the end but rather the beginning of our endeavors aimed at fostering corporate growth and embracing ESG-oriented management, as we strive toward the sustained growth of our Group.
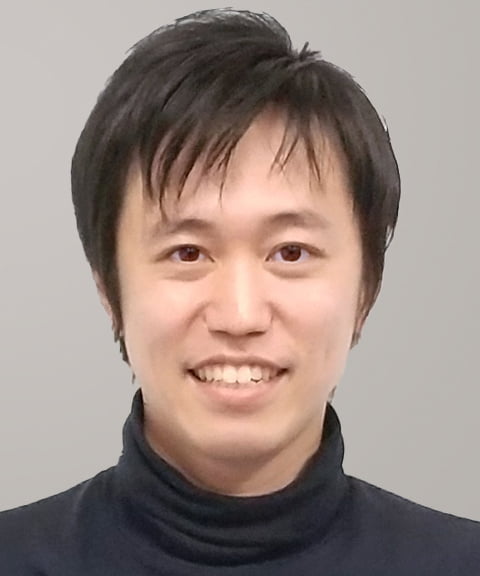
Implementation of an LCA Calculation Method Across Japan Group
Encouragement Award winner: Yuji Matsushita (The Spokesperson for the Award Winners)
Japan Group Life Cycle Assessment - Working Group
Life Cycle Assessment (LCA) serves as a method for quantifying the environmental impact of each of our products in terms of numerical values and data. In 2022, we initiated the LCA Working Group (WG), comprised of cross-functional members from within Japan Group, leading to the development of an LCA methodology. Our efforts were executed with a strong focus on two key aspects of VITALS: Vigilance and Teamwork. In terms of Vigilance, a significant driving force for the WG was the realization that we might not be adequately prepared to address contemporary megatrends like decarbonization and sustainability. As for Teamwork, each member of the WG collectively shared the objective of meeting the requirements of external stakeholders. Building upon this shared objective, we defined the specific roles of each team member, a step we believe greatly contributed to our effective teamwork.
We firmly believe that assessing the environmental impact of our products and striving to transform that impact into a positive one constitutes a significant stride toward realizing our Purpose of enriching the world, transcending our contributions to sales and profits.
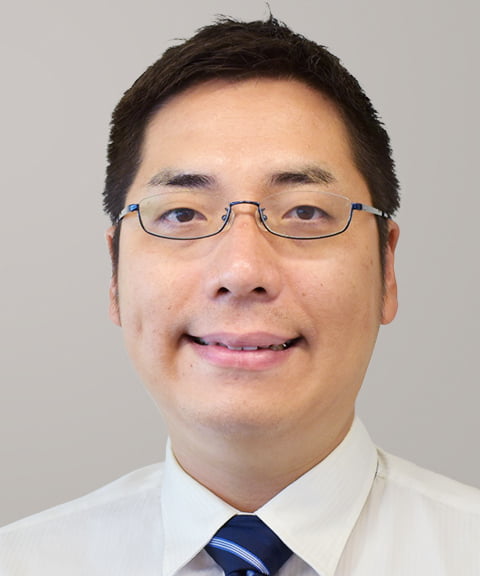
Providing Worksite-Oriented Legal Services Beyond PC and Department Boundaries
Encouragement Award winner: Katsutoshi Ando (The Spokesperson for the Award Winners)
Legal Department
In accordance with the principles of “J-LFG” and “VITALS,” the Legal Department has developed several activity plans, guided by two key policies: “Leveraging our extensive network of PCs and other departments to actively facilitate interdepartmental collaboration,” and “Engaging with our Group’s business operations through on-site visits to proactively fulfill our responsibilities.” As part of one action plan, members of the Legal Department visited individual PCs and collaborated directly with their staff. This approach facilitated the delivery of legal services that are highly tailored and beneficial to the PCs, enabling the prompt identification of legal risks and the presentation of effective solutions. We opted to offer in-person services to PCs instead of online services, as this approach helps elevate the visibility of the Legal Department, enhances communication, enables us to precisely grasp facts, and fosters a sense of ease. We consider this sense of ease to be a fundamental factor contributing to our commendable performance. As a group of legal experts with a deep understanding of our Group’s business, the Legal Department will persist in the quest for the most optimal and effective means of supporting the businesses in Japan Group.
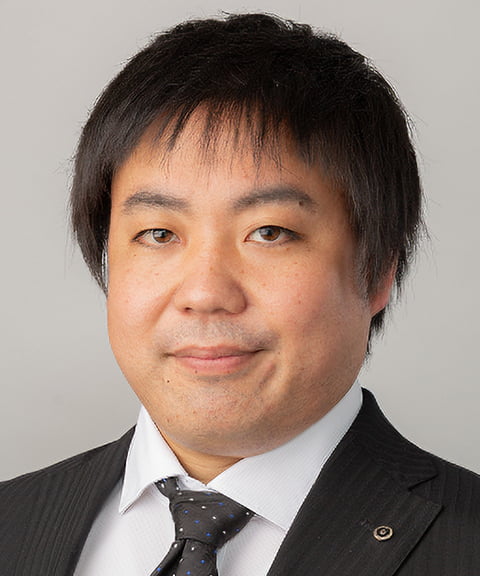
Driving Growth and Value Enhancement in Nippon Paint Group Through J-LFG Integration
The Co-President Award winner: Yasufumi Suzuki (The Spokesperson for the Award Winners)
Business Strategy Promotion Office,
Nippon Paint Co., Ltd.
Initially, we contemplated the essential requirements for leveraging J-LFG to foster growth and enhance value of Nippon Paint Group. Our conclusion emphasized the pivotal importance of instilling a collective awareness among all employees, encouraging them to recognize the significance of J-LFG and translate this understanding into action. The “recognition and understanding” phase plays a critical role in expeditiously integrating J-LFG within the group. Therefore, we undertook a multitude of initiatives, including the creation of awareness posters, dissemination of messages from the management, and organization of briefings for department heads. We are confident that these initiatives have enhanced employees’ comprehension of J-LFG and VITALS, resulting in record high number of entries for the J-LFG Awards.
We have initiated fresh endeavors aimed at raising awareness of J-LFG, with a particular emphasis on not just increasing the quantity of entries for the J-LFG Awards, but also enhancing the quality and diversity of themes submitted. Our commitment remains steadfast in nurturing a new culture in the NPTU Group. We aspire to achieve this through activities that promote a sound understanding of J-LFG and inspire individuals to embody this culture in their conduct.