SDGs(持続可能な開発目標)の実現に向け、自動車業界においても環境負荷の低減が求められています。自動車部品の製造においては、塗装工程を削減することが最もCO2排出量の低減につながると言われている中、これまでの塗装方法を変えるとしたら何ができるかという発想から、型内塗装技術の開発がスタートしました。100年に一度の大変革期を迎えている自動車業界に革新をもたらしたいという思いから始まった今回の開発。キーパーソンとなる開発・営業担当者たちの挑戦をご紹介します。
樹脂成形と表面塗装を一工程にすることでCO2を大幅削減日本ペイント・オートモーティブコーティングス株式会社(以下、NPAC)と自動車の外装部品などを手掛ける内浜化成株式会社が共同で開発した型内塗装は、自動車の樹脂部品を成形する際に金型内に塗料を注入し、樹脂成形と表面塗装を一工程で行う技術です。これにより、製造工程の短縮やCO2排出量の削減に貢献します。この型内塗装に適した塗料としてNPACが開発したのは、VOC(揮発性有機化合物)をほとんど含まない無溶剤型で、環境にも配慮したうえで従来の塗装品質を担保した新たな製造プロセス提案となっています。
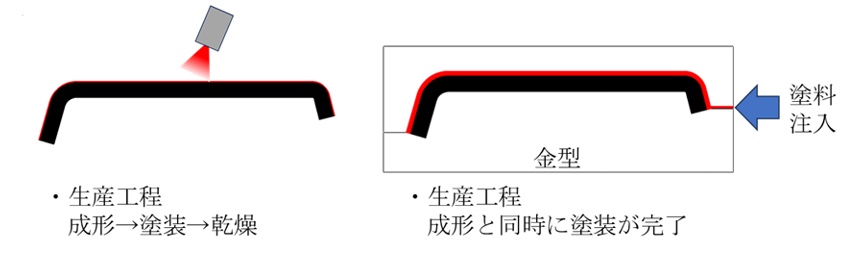
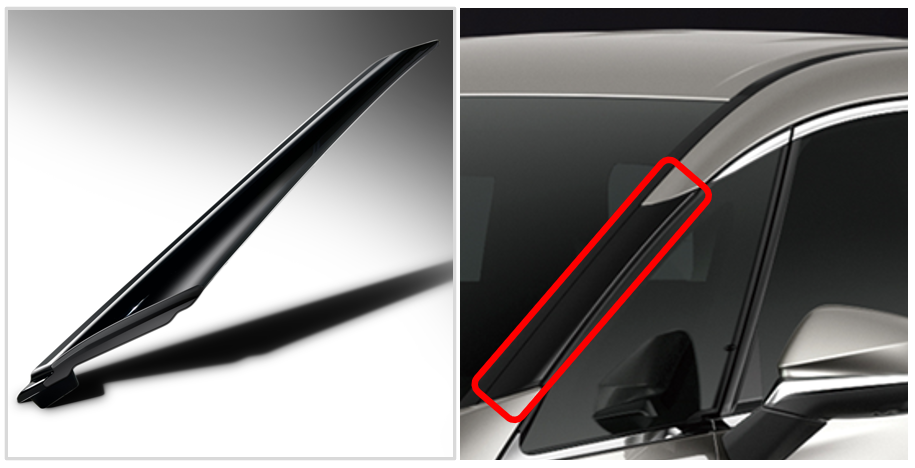
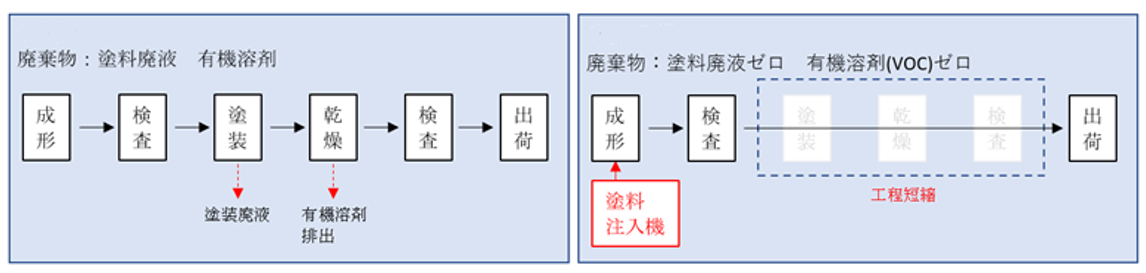
すべての設計を見直すところから開発がスタート
2018年から開発に着手した型内塗装に使用する塗料は、既存のものとはコンセプトが全く異なるため、すべての設計を見直すところから始まりました。まず、コンセプトを基に無溶剤かつ金型内で硬化可能な仕組みをどのように実現するかを考え、スペックに照らし合わせながら物性を最適化していきました。しかし、溶剤を使用しないという制約があったため、適用可能な塗料材料が限られる点が設計上の課題となりました。「外部の試験機関にも2年ほど通いながら、トライ&エラーを繰り返すことで完成度を徐々に高めていくことができました」と開発担当者は振り返ります。
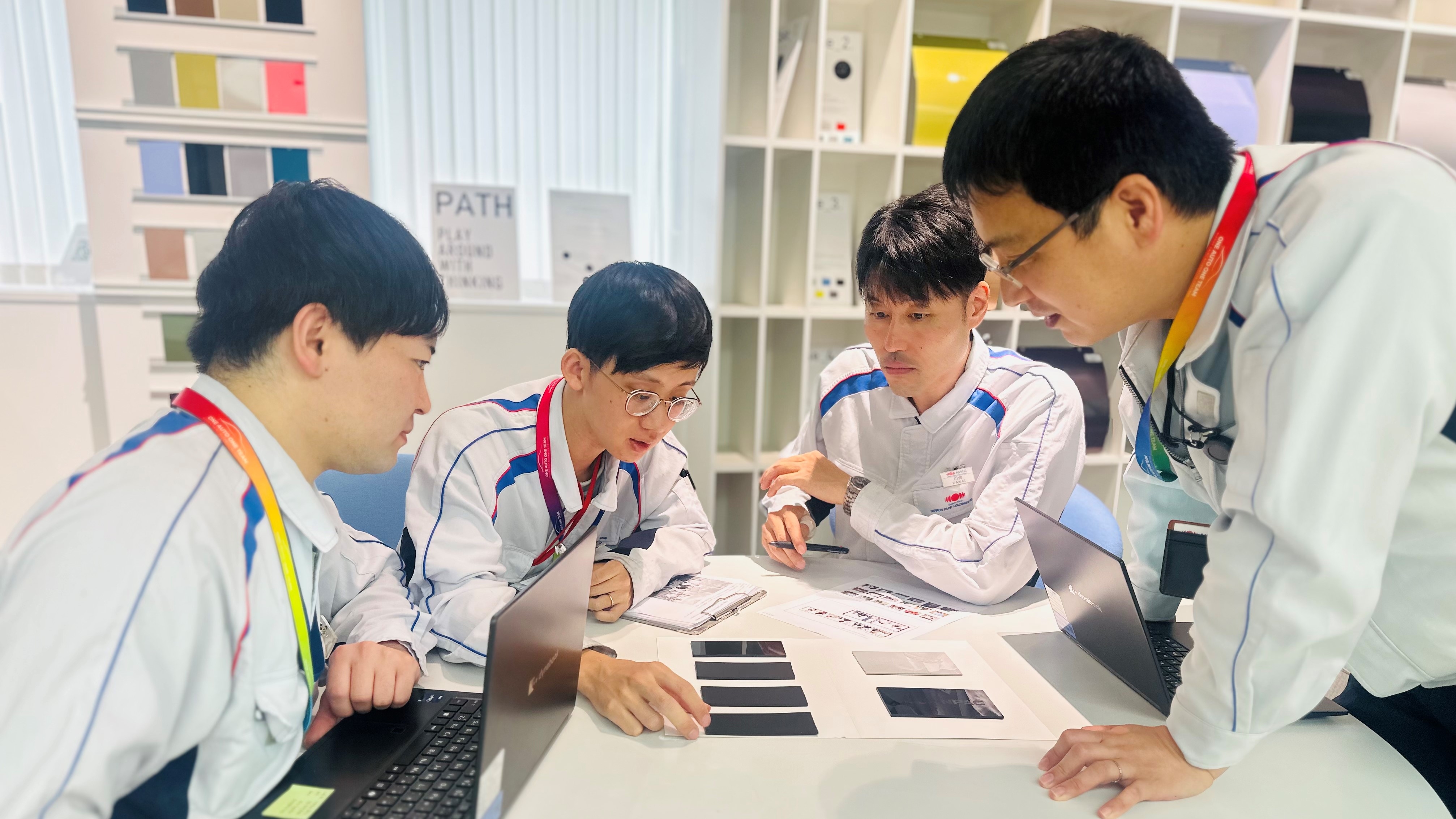
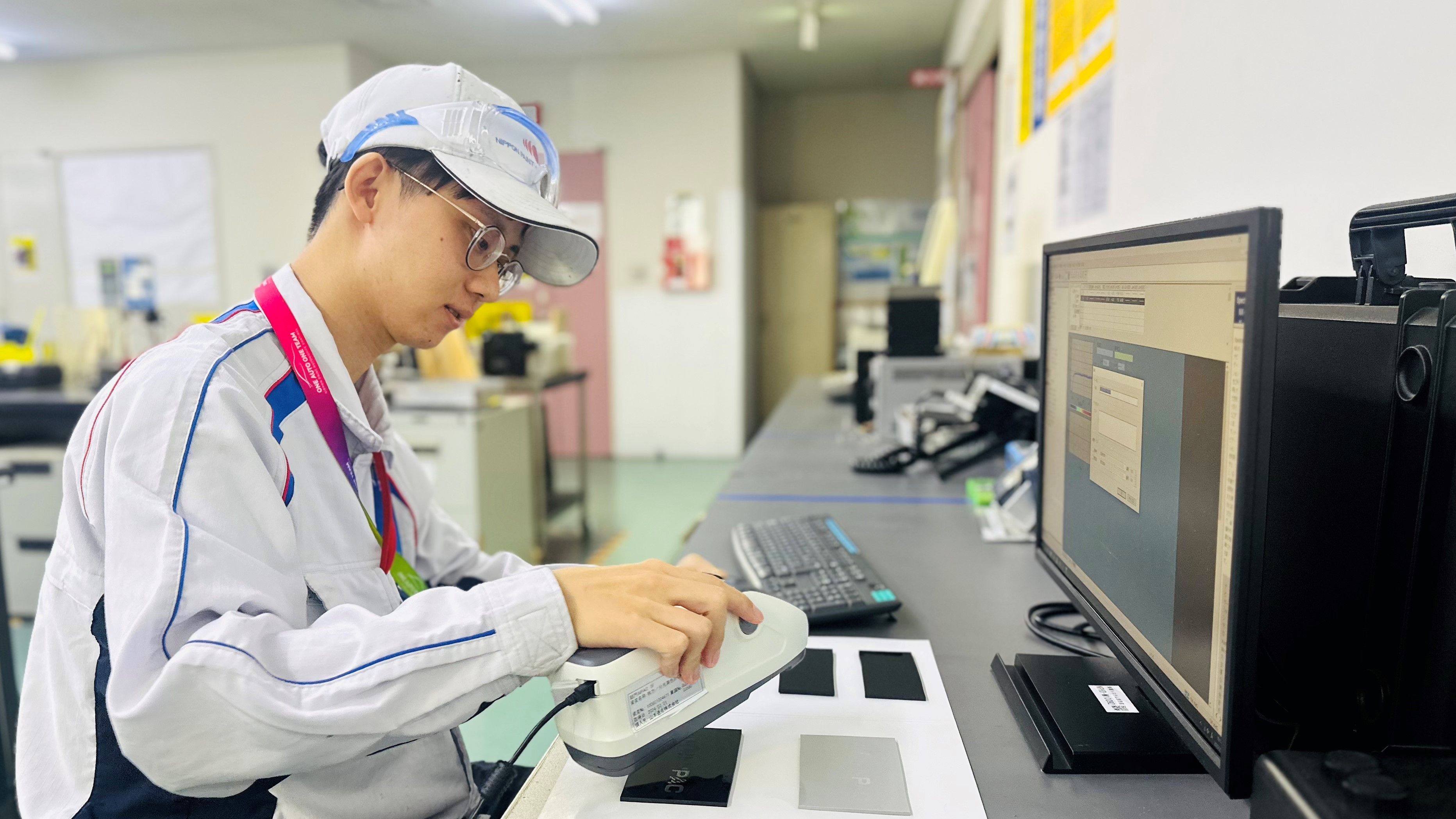
もともと、NPACではスプレー塗装用の塗料を通じて内浜化成と協業しており、その中で成形物に加飾するだけではなく、カーボンニュートラルにも対応した塗装技術を確立したいという思いが両社で一致し、共同開発に至った経緯があります。今回開発した型内塗装技術は、国内で唯一、大型の熱可塑性樹脂部品に対応しています。熱可塑性樹脂は加熱すると溶融し、冷却すると硬化する特性を持っています。金属よりも軽量でありながら耐久性や強度を維持することができ、燃費向上の観点からも自動車の外装部品に幅広く採用されているものです。
型内塗装に用いる塗料は、金型内に塗り広がるまでは固まらず、金型内に充填した後はすぐに硬化して固まることが求められます。小さい金型(部品)の場合は、塗り終わるまでの時間が掛からないため比較的容易ですが、金型が大きくなればなるほど、塗料を流し込む粘度制御や設備面での難易度は上がります。「塗料に使われる材料の配合を考えることも重要ですが、塗料メーカーだけでは解決できない設備面は、内浜化成と一緒に解決していきました。内浜化成の金型を使った射出成形のノウハウを活用するとともに、金型構造や塗料注入設備の最適化によって、技術の確立にまた一歩、近づけることができました」と開発担当者は説明します。
屋外耐候性試験にも大きなハードル屋外耐候性の評価プロセスにおいても大きな壁がありました。自動車の外装部品に求められる耐候性のレベルは非常に高く、複数年にわたり経年劣化を実際の屋外環境で観察する曝露試験が必要になります。太陽光や風雨が要因となる経年劣化を評価する際は、開発をよりスピーディーに進めるため、屋外環境を人工的に再現できる促進耐候性試験機を活用することが一般的です。まずは、試験機の評価結果をベースに開発を進め、一定の基準をクリアすることができました。しかし、長期にわたる曝露試験では思うような結果が得られず、実際の屋外環境の厳しさを改めて痛感することとなりました。
そこで、より実際の屋外環境に近い評価方法を模索するため、国内外のさまざまな耐候性試験やスペックを比較検討しました。そして今回の開発において屋外環境に最も近い結果が得られる評価方法を見出し、その評価方法を取り入れながら、曝露試験と促進耐候性試験を同時に進めていきました。「少しでも早く結果を出すために、曝露試験を行う沖縄への輸送手段を船便から航空便に切り替えて、評価を終えたサンプルを見て一喜一憂しながら、試行錯誤を重ねました。」また、見た目では分かりにくい塗料の性能を正確に把握するため、ミクロレベルまで詳細な分析を実施しました。こうして得られたデータから劣化要因を予測し、設計を見直しながら、チーム一丸となって検討を重ね、一つずつ課題をクリアしていきました。
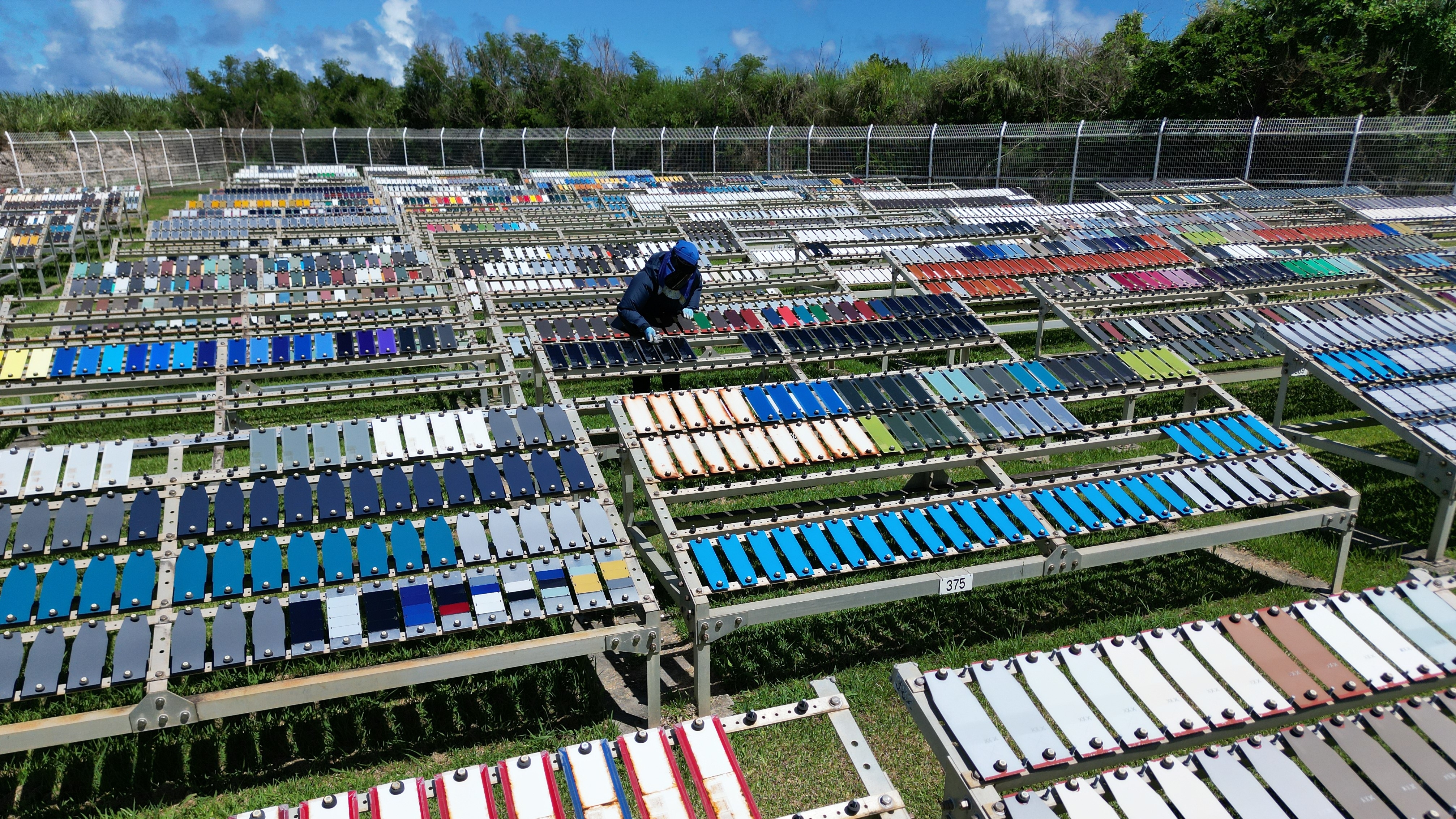
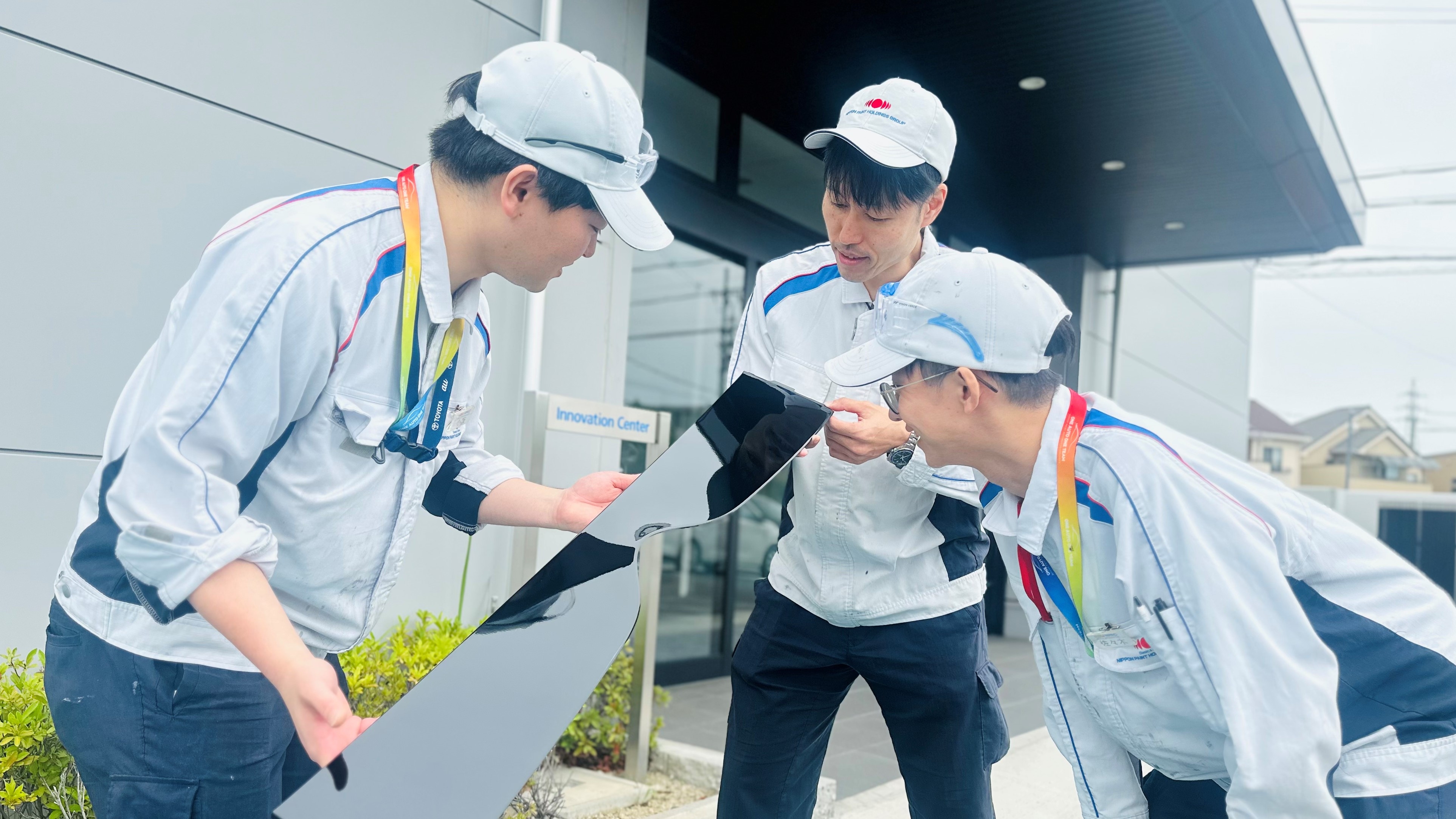
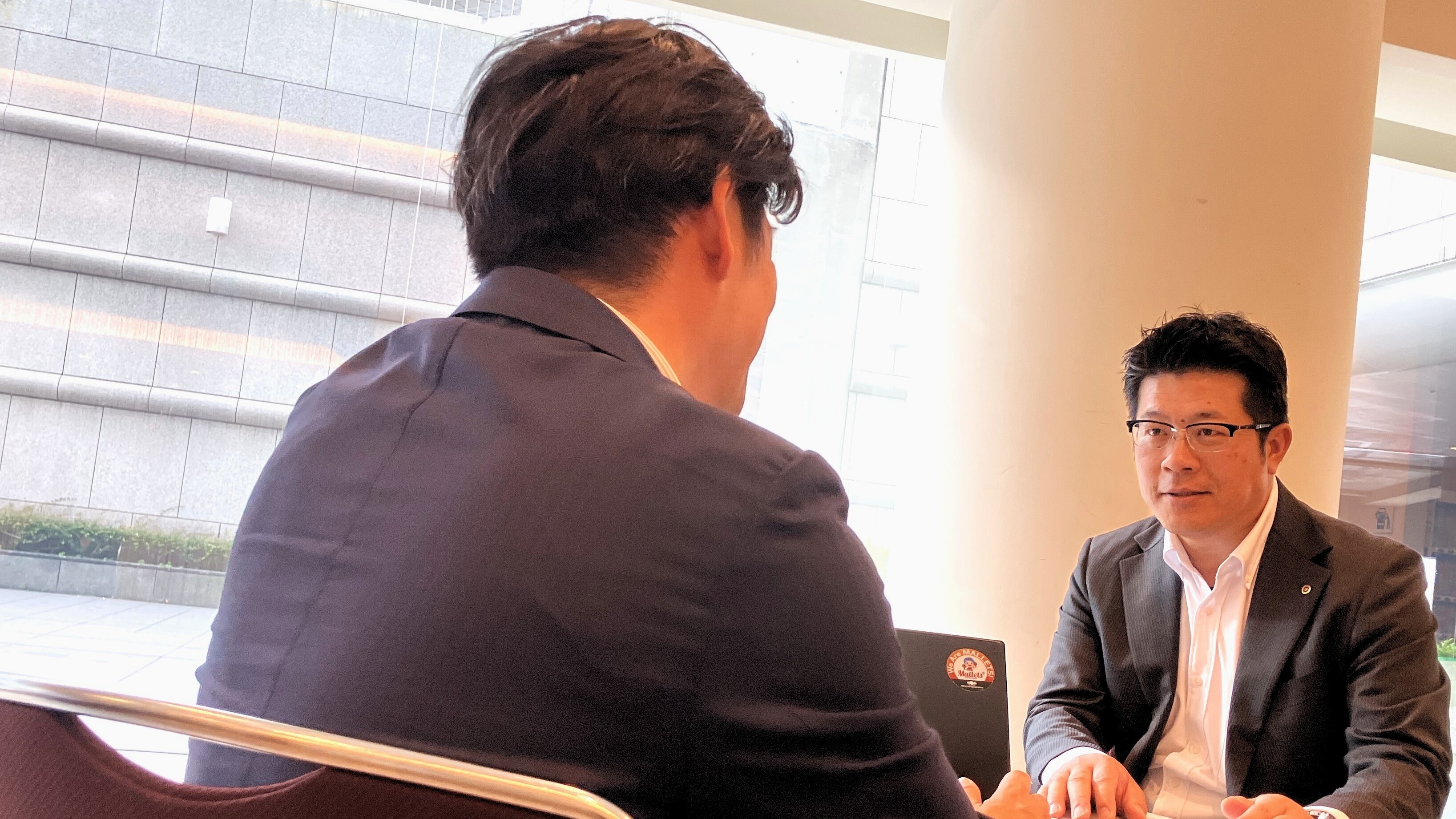
塗料メーカーとしての配合・設計面からのアプローチはもちろん、乾燥時間や温度など諸条件を最適化し、内浜化成やその先のお客様となる自動車メーカーともコミュニケーションをとりつつ、曝露試験を繰り返してベストな着地点を見つけていきました。「自分たちだけでは挫折していたかもしれませんが、内浜化成との信頼関係のもと、お互いが良い緊張感を持ちながら支え合うことが課題解決につながりました」と営業担当者は振り返ります。「両社が同志として最後まで形にしようという強い思いを持ちながら、その先の自動車メーカーとも一体となった技術共有、対話があったからこそ、難関となる試験を何とかクリアすることができました。」
型内塗装は金型内に彫り込んだ模様を精密に転写する仕組みのため、従来は再現できなかった多様なデザイン表現が可能になるという利点があります。さらに、一般的なスプレー塗装に比べて高い表面平滑性も実現します。「特に塗料メーカーとして挙げられる優位性は、無溶剤化によりVOCの排出を徹底的に抑えている点です。外装用の厳しいスペックを確実にクリアするだけでなく、新技術としてそれ以上の品質検査評価にも多数合格しています」と開発担当者は強調します。また、従来の方法に比べてCO2の排出量削減や光熱費を低減していることも特徴の一つとなっています。さらに、塗装ブースや乾燥炉が不要になるので、設備スペースの削減も実現します。これまでは、乾燥工程に1時間ほどかかりましたが、型内塗装では金型の中で塗装が完結し、時間も1分以内で完了します。これらを達成するために、塗料の配合面だけでなく、成形条件からもアプローチしたことが成功の大きな要因となりました。
ナノレベルの凹凸構造を利用した光干渉による虹色発色(顔料不使用)
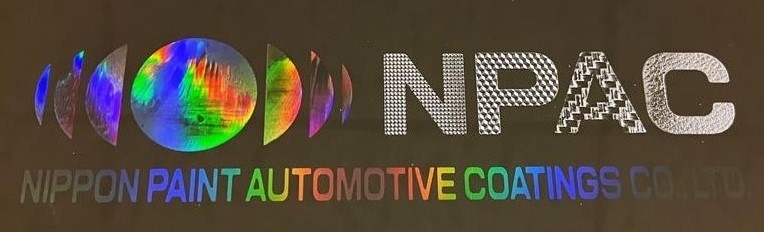
(左:スプレー塗装/右:型内塗装)
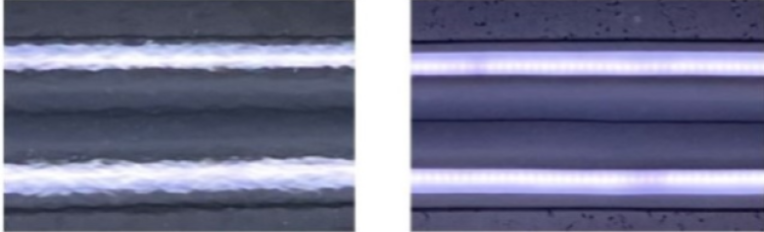
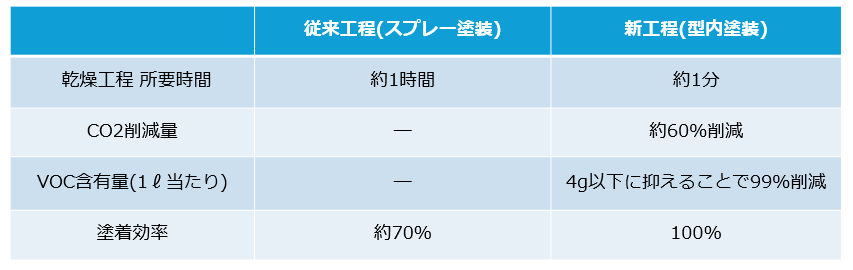
型内塗装ならではの価値を提案
今後の展望について、営業担当者は次のように話します。「型内塗装部品をより多くのお客様に採用していただくことが直近の目標です。自分が携わってきた技術を車に乗せたいという強い気持ちで日々取り組んでいます。型内塗装だからこそ実現できる外観の美しさや独自の意匠性を強みとして掲げ、価値訴求を行っていきます。また、環境への配慮を実感していただければ、企業の社会的責任を果たすうえでご評価いただける技術だと確信しています。」開発面での将来的な目標については「現状は黒色の大型外装部品がターゲットですが、多色展開も目指していきたい」と話しました。型内塗装部品の量産化はまだ始まったばかり。自動車の製造工程に革新をもたらす次世代技術として、さらなる製品の開発、実装に向け提案を続けていきます。
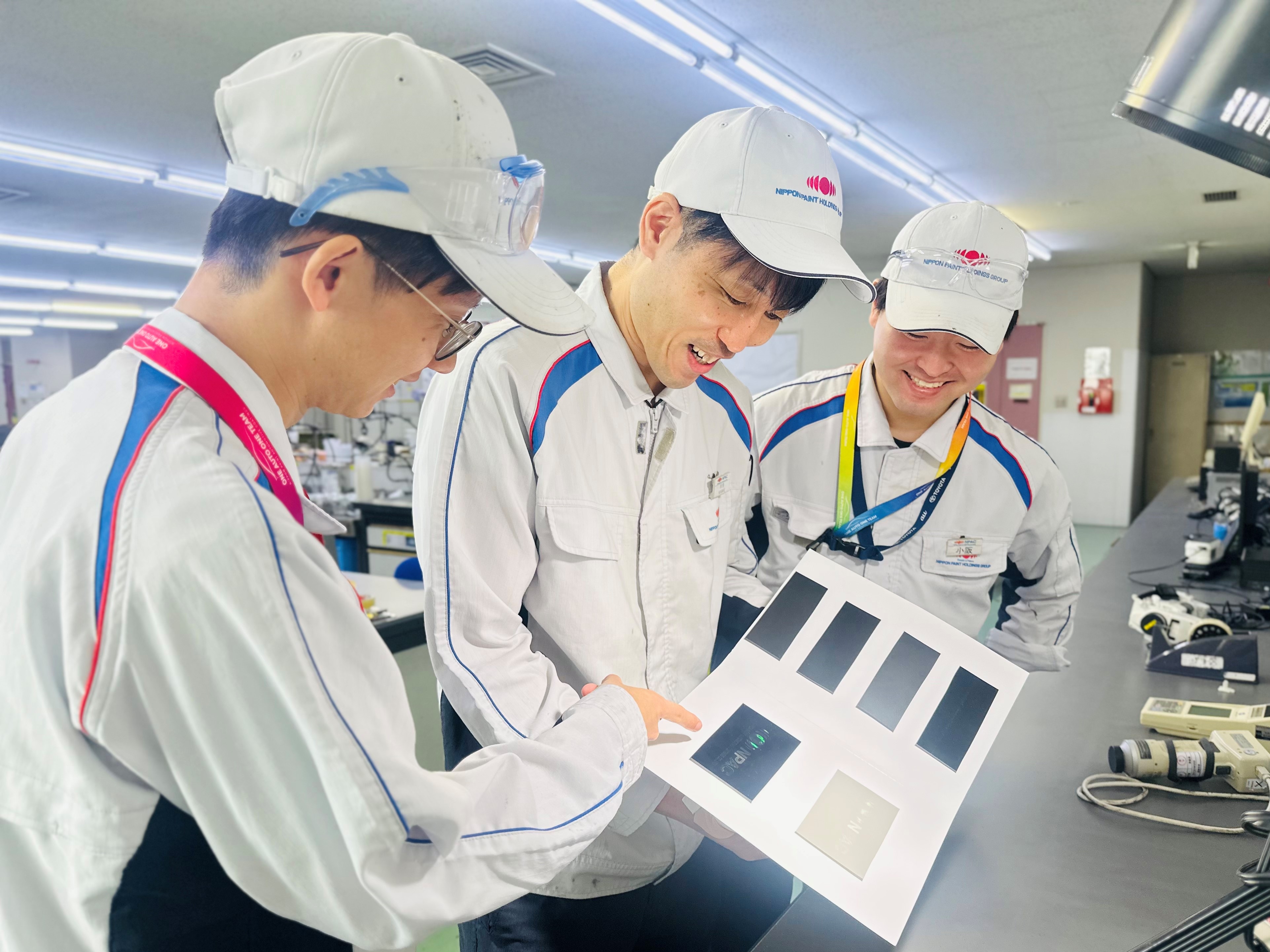
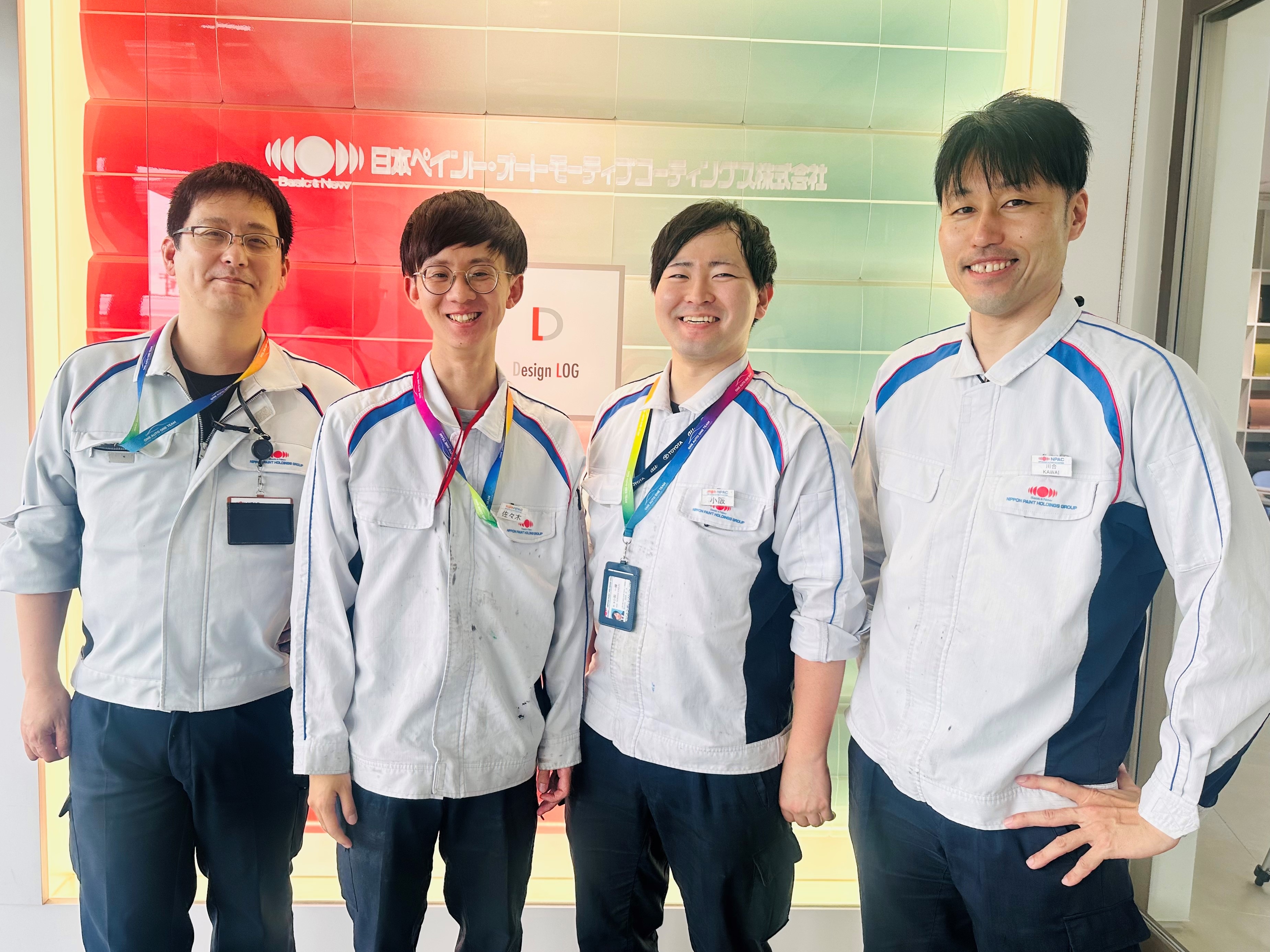
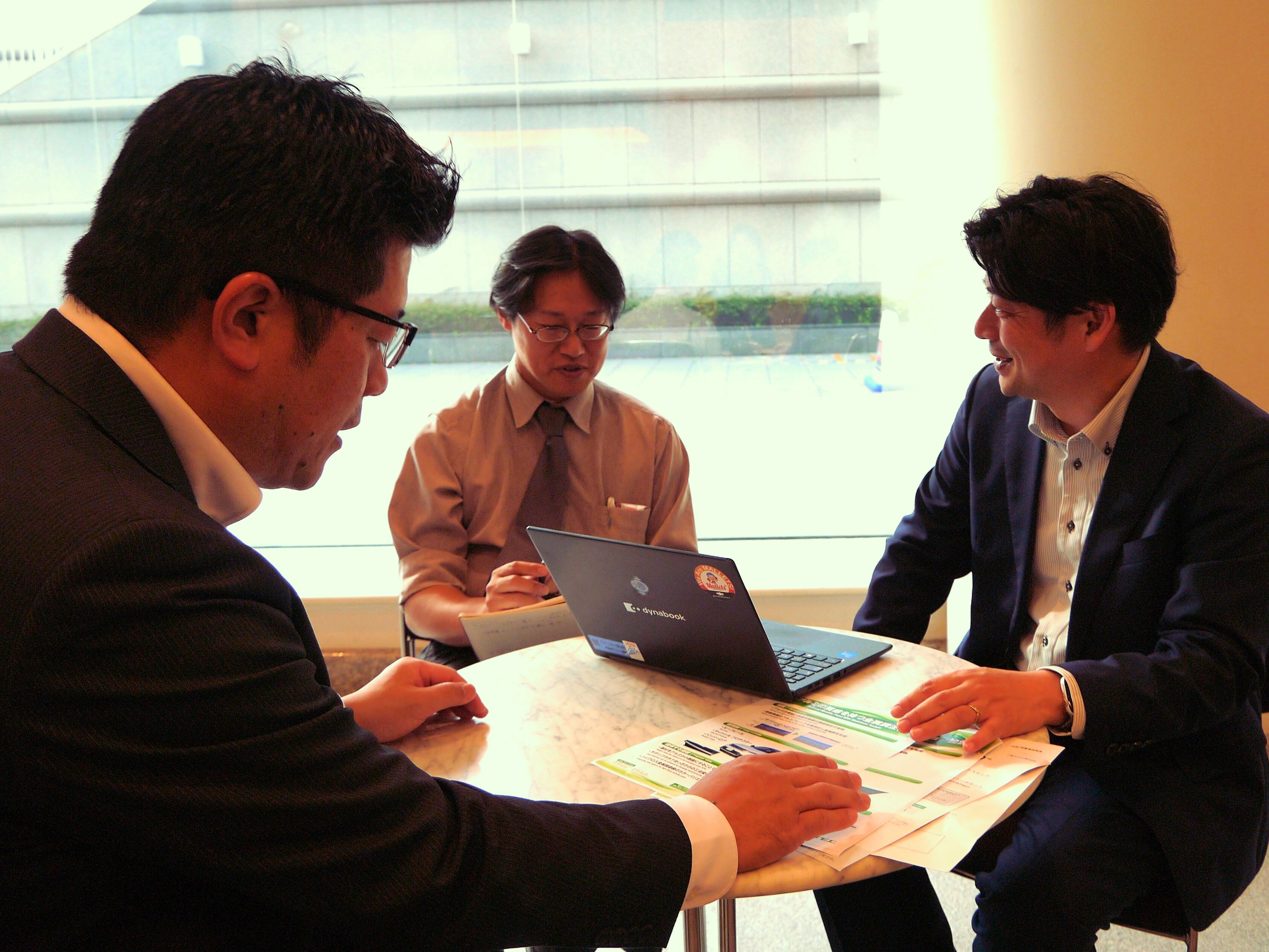
型内塗装技術について、詳しくはこちらをご覧ください